Durezza è la
resistenza meccanica , un materiale della penetrazione meccanica di un corpo di prova più duro oppone. A seconda del tipo di azione è diverso a diversi tipi di durezza. Dom durezza non è solo la resistenza al corpo duro ma anche contro morbida, il corpo rigido. La definizione di durezza diversa da quella di
resistenza , che è la resistenza di un materiale alla deformazione e separazione.
La durezza è una misura della
resistenza all'usura dei materiali. Rigidi
lenti graffiare meno, temprati
ingranaggi si consumano di meno. Nella scelta degli
utensili da taglio , come testa di fresatura o
strumento tornio , la durezza di particolare importanza, il taglio è difficile rimanere vivi più a lungo, ma rompere più veloce.
Durezza e test sono un elemento centrale nel campo della
fisica dello stato solido ,
scienza dei materiali e l'analisi dei
materiali e in
scienze della terra per la caratterizzazione di
rocce e
minerali . Durezza è uno dei
tenacità ,
resistenza ,
duttilità ,
la rigidità ,
la densità , e la
temperatura di fusione delle
proprietà del materiale di un materiale.

Prova di durezza su un rotolo nel 1900
- 1 durezza e resistenza
- 2 prova di durezza e durezza scale
- 2,1 durezza Martens prova universale (durezza)
- 2,2 di prova di durezza Rockwell (HR)
- 2,3 Prova di durezza Brinell
- 2,4 Vickers prova di durezza (HV)
- 2,5 prova di durezza Knoop
- 2,6 prova di durezza Shore
- 2,7 Test di durezza Barcol
- 2,8 Test di durezza Buchholz
- 2,9 Leeb Prova di durezza
- 2,10 durezza Mohs di prova
- 02:11 prova di durezza più speciale
- 3 unità
- 4 disagi e tranciatura
- 5 rivalutazione
- 6 Vedi anche
- 7 Collegamenti esterni
- 8 Note e riferimenti
|
Durezza e forza [ Modifica ]
La durezza di un materiale è solo parzialmente qualcosa con
forza per fare del materiale, anche se la forza dei metodi di prova per misurare la durezza, la profondità di penetrazione sui vari
campioni di prova sono basati influenzati. L'influenza della resistenza può essere ottenuto mediante misurazione di
film sottili ridotta, ma non completamente evitati.
In alcuni casi, la durezza di un materiale è, tuttavia, in un umwertbaren relativa a forza materiale. Poi dalla prova di durezza relativamente poco costoso di solito molto più costoso
prova di trazione vengono sostituiti. Di importanza pratica è la possibilità di effettuare una nuova valutazione della durezza Vickers Brinell e sulla resistenza alla trazione di acciai strutturali. Così, per esempio, in prove su strutture in acciaio possono essere rilevati confusione materiale.
Molti materiali hanno elevata durezza ed elevata
fragilità , possono quindi difficilmente deformarsi plasticamente e improvvisamente collassare. Questa è la base, tra l'altro, la tecnica di
taglio del vetro .
Per la costruzione dei componenti deve essere equilibrata durezza e tenacità senso: La rigido, componente fragile rompe facilmente, una volta che si verifica un carico di punta. Tough (meno dura) materiale sarebbe senza danno o con solo piccoli effetti. Nel secondo caso si consumano molto velocemente. Lo scopo è, pertanto, spesso, una grande area interna (core) in robusto, resistente materiale con uno strato superficiale molto difficile da prevedere. Questo ha due vantaggi: La resistenza all'usura aumenta e crepe possono formare molto peggio. I carichi effettivi sono riprese in esterni.
Prova di durezza e durezza scale [ Modifica ]
Nella scienza dei materiali, in particolare nei metalli, metodi di prova utilizzati sono principalmente ciò che il
rientro misura. In questo i campioni di prova standard vengono premuti, alle condizioni stabilite nel pezzo. Seguendo la superficie o la profondità della rientranza permanente viene misurata. In linea di principio, viene fatta una distinzione statica e dinamica metodi di prova di durezza. I metodi di prova dinamici per portare il carico sul pezzo da controllare in un tratto, nel metodo statico, il carico è costante o lentamente aumentando.
Martens prova di durezza (durezza universale) [ modifica ]
Il nome di durezza universale smentisce il reale utilizzo in ambienti industriali. Lì, e anche in laboratorio questo metodo è usato molto raramente.
La durezza Martens prova era dal fisico tedesco
Adolf Martens nome (1850-1914) ed è anche chiamato indentazione strumentata. Nel 2003, la durezza universale è stata ribattezzata la durezza Martens. Il processo è descritto nella norma ISO 14577 (Materiali metallici - rientro di prova strumentato per i parametri di durezza e materiali) standardizzato.
In questo metodo, durante il
carico - continuamente e fase di scarica, la forza e la profondità di penetrazione misurata. La durezza Martens (HM) è definita come il rapporto tra la forza massima specificata per l'area di contatto corrispondente e in Newton per millimetro quadrato.
A differenza del Vickers o Brinellverfahren è determinato non solo il comportamento plastico del materiale, ma dalla curva di misura ottenuta può anche parametri dei materiali, come il
rientro (rientro elastico - E
IT ), che
Eindringkriechen (C
IT ) e plastica elastica e
deformazione plastica può essere determinato.
Come penetratore stanno seguendo le forme più comuni: la piramide Vickers (vedere il metodo Vickers), una sfera di metallo duro, un diamante penetratore sferico e il penetratore Berkovich. Il penetratore Berkovich ha una punta come un normale
tetraedro . bordo con angolo di 65 ° Il contorno delle impressioni è tipicamente approssimativamente triangolare.
[1]
La conversione della profondità di penetrazione della superficie di contatto deve essere determinato per ciascun Eindringkörperform. L'area di contatto è calcolata per il corpo Vickers e Berkovich dal prodotto del quadrato della profondità di penetrazione e la costante di 26,43.
Test di durezza Rockwell (HR) [ modifica ]
Ci sono diversi dell'ingegnere americano e fondatore
Stanley Rockwell nel
1920 i metodi di prova di durezza sviluppati che sono specializzati per determinati settori. Le procedure sono differenti con l'unità
HR e in una successiva identificazione; esempi di designazione sono Rockwell HRA, HRB, HRC
[2] o HR15N in prova di durezza su fogli fino ad uno spessore di 0,20 mm e oltre HR15T HR30Tm.
La durezza Rockwell di un materiale risultante dalla profondità di penetrazione di un campione a richiesta di un particolare carico pre-e test. Campioni, le forze, la durata, e le formule di unità sono definiti nella norma DIN EN ISO 6508-1 (ex DIN EN 10109). Con un carico di prova predeterminato, il campione è polarizzato nella superficie del pezzo da testare. La profondità di penetrazione del provino viene utilizzato come pre-carico nel piano di riferimento. Poi il penetratore per un periodo di almeno due secondi, e un massimo di sei secondi viene caricato con il carico principale. Allora questa viene rimossa, in modo che solo il pre-carico è efficace. La differenza di profondità di penetrazione prima e dopo il posizionamento del carico principale è una misura della durezza Rockwell del materiale. Le
unità Rockwell calcolato dopo (a seconda applicata Normskale diverso) formula dalla profondità di penetrazione. La profondità di penetrazione del provino è a un
indicatore rilevato che è collegato alla sonda.
Nel metodo di C scala (unità HRC) a è
a forma di cono provini di
diamante con un angolo di punta di 120 ° ed una punta arrotondata con un raggio di 0,2 mm viene utilizzato (la C sta per la parola inglese
cono per "cono"). Questo metodo viene utilizzato principalmente per materiali molto duri vengono utilizzati. Come altre sfere di metallo duro Rockwelleindringkörper vengono utilizzati con un diametro di 1,5875 millimetri (HRB, HRF, HRG) o 3,175 millimetri (HRE, e SAR HRK).
Esperimento:
- Pre-carico (dare al HRA, HRB, HRC, ecc: 10 kg (~ 98 N) a HRN e HRT: 3 kp (~ 29,4 N)
- Calibro a zero
- Forza principale, oltre a rinunciare (ad esempio, HRB = 90 kp (~ 882,6 N), HRC = 140 kp (~ 1372,9 N))
- Tempo di esposizione dipende dal comportamento allo scorrimento del materiale:
2 s - 3 s
per metalli senza tempo-dipendente comportamento plastico
3 s - 6 s
per i metalli con dipendenti dal tempo comportamento plastico
- Forza abrogazione principale
- Durezza valore letto dal comparatore
- Pre-carico di raccogliere
La prova Rockwell è molto veloce, ma richiede prestazioni elevate sul serraggio del campione nell'apparecchio di prova. Non è adatto per campioni che producono il tester elastico, per esempio,
tubi .
Esempi di durezza Rockwell:
Sopra 65 HRC solito infinite possibilità per la lavorazione con definiti taglienti
[3] delle superfici (tornitura, foratura, fresatura), più dure superfici devono essere levigato (lavorazione con taglienti geometricamente definiti).
Campo di misura: ammesso per il processo di valori di durezza sono 20 <HRC <bugia 70
Prova di durezza Brinell [ Modifica ]

Kugelschlaghärteprüfgerät
Con l'ingegnere svedese
Johan agosto Brinell nel 1900 e sviluppato la
esposizione mondiale di Parigi ha presentato il metodo di prova di durezza viene utilizzato in metalli duri morbidi e medio (DIN EN
ISO 6506-1 e ISO 6506-4) come acciaio dolce, leghe di alluminio, in legno (ISO 3350) e per materiali a struttura eterogenea, come la ghisa, viene utilizzato. Qui, è una
sfera in metallo duro con un carico di prova fisso
F premuto sulla superficie del pezzo di prova.
In precedenza, come aggiunta alla palle penetratore carburo e sfere di acciaio utilizzato. Dopo lo stato finale di standardizzazione, una sfera d'acciaio a partire dal 2006, tuttavia, non è più consentito. La norma prevede ora per tutte le palle le sostanze
di metallo duro prima. Le perle utilizzati hanno un diametro di 10 mm, 5 mm, 2,5 mm, 2 mm e 1 mm.
Dopo un tempo di esposizione di 10 a 15 secondi per
acciai e
ghisa , e da 10 a 180 secondi per i
metalli non ferrosi e loro leghe, il diametro della rientranza permanente è misurata nel pezzo e determina la superficie dell'impronta. Per essere determinato è il diametro d media di due diametri perpendicolari reciprocamente
d 1 e
d 2 dell'impronta permanente. In
anisotropo deformazione della durezza necessaria per calcolare il diametro più grande è
d 1 e piccolo diametro
d 2 media.

La
durezza Brinell è definito come il rapporto tra il carico di prova alla superficie impressione. La forza di prova in
Newton è moltiplicato per il valore di 0,102 (cioè l'inverso di 9,81) per l'alimentazione di unità
Newton nella precedente unità
Kilopond convertire. Questo assicura che le misurazioni di durezza con unità moderne producono lo stesso risultato come valori storici basata su unità oggi obsolete.

Nella formula precedente, la forza F è in
N , la palla diametro D, e la media impressione diametro d in mm. Il valore dei risultati denominatore della formula per la superficie della faccia circolare di un segmento sferico, una cosiddetta
calotta .
Specifica standardizzata di durezza [ Modifica ]
Secondo la norma DIN EN ISO 6506-1 a partire dal 03/2006 deve essere vicino al valore di durezza e il metodo utilizzato, il diametro della sfera e il carico di prova deve essere sempre specificato con.
- Esempio: 345 HBW 10/3000
in cui:
- 345 = valore di durezza
- HBW = procedura [4] (W è il materiale della palla di prova: carburo di tungsteno)
- 10 = diametro della sfera D in mm
- 3000 = Forza di prova in kp
Con un carico che richiede più di 15 secondi, il tempo di caricamento è dato anche. Esempio: 210 HBW 5/10/60
È una modifica delle prove con il Brinell
Poldi martello , in cui è formata l'impressione della palla da un martello indefinito mano. A causa del carico improvviso è una prova di durezza dinamica. Il pallone entra posteriore in una asta di metallo con una durezza definito. Dal rapporto tra il diametro indentazione poi la durezza del campione può essere calcolata. Il metodo ha il vantaggio che può arbitrariamente montato esemplari e componenti costruiti può essere controllato localmente. I valori di durezza così determinati non corrispondono esattamente i valori di durezza determinati staticamente per le affermazioni fatte nel settore, ma sono sufficienti nella maggior parte dei casi. Il termine "Poldi" deriva dalla pianta stesso acciaio in lingua ceca
Kladno , dove questo metodo di test è stato sviluppato.
Con acciai non legati e basso possibile dal Brinell con certa tolleranza della
resistenza alla trazione (
R m ) del materiale può essere derivata.
R m ~ 3,5 × HBW
Durezza Vickers di prova (HV) [ modifica ]

Un non-standard di impronta (sbagliato) di un tester Vickers inciso in
acciaio temprato
Il
test Brinell è molto simile a quello nel 1925 da Smith e Sandland e sviluppato dalla società aerospaziale britannica
Vickers test chiamato durezza, che viene utilizzato per il test di materiali omogenei ed è utilizzato anche per testare la durezza superficiale o sottili induriti pezzi e bordi. E 'nella norma DIN EN ISO 6507-1:2005 per -4:2005
[5] controllato. In contrasto con la prova Rockwell è un triangolo equilatero
piramide di diamante con un angolo di apertura di 136 ° viene premuto con una forza di prova predeterminato al pezzo. Dal rilevata per mezzo di un microscopio di misura della lunghezza della diagonale del rientro impressione permanente la superficie è calcolato. Il rapporto di forza di prova in Newton sulla superficie impressione (
d in millimetri) viene moltiplicato per un fattore di 0,1891, la durezza Vickers (HV, Eng. VHN =
durezza Vickers Number ). È stato sviluppato come prova di durezza, era pratica comune per specificare la forza di prova in newton dell'unità, e il fattore era 1,8544 (= 2 * sin 136 ° / 2).

è qui

Il numero 0,102 è la conversione di Newton in newton.
La prova di durezza Vickers è suddiviso in tre aree:
- Prova di durezza Vickers: F 49,03 N ≥
- Prova di durezza Vickers piccola forza: 1961 N = F <49,03 N
- Microdurezza Vickers di prova: 0.098 N = F <1,961 N
Specifica standardizzata della durezza Vickers [ Modifica ]
Oltre al valore di durezza è anche utilizzato il metodo di prova ed il carico di prova deve sempre essere specificato con.
- Esempio: 610 HV 10
in cui:
- 610 = valore di durezza
- HV = processo
- 10 = forza di prova F in newton
Con un carico che non ultimi 10 o 15 s, il tempo di caricamento sono anche dato. Esempio: 610 HV 10/30
La prova Vickers viene normalmente eseguita ad una unità di prova fissa, che non ondeggi, o può essere disturbato. Per testare componenti di grandi dimensioni e / o solido, è anche durometri portatili, che sono magneticamente o meccanicamente collegati o sul provino.
La prova di durezza Vickers è versatile ed è un quasi-test non distruttivi, poiché solo una piccola parte del danno, che spesso possono essere accettate. I componenti che non mostrano alcun danno dopo il test, è considerato un metodi di prova distruttivi, perché il componente viene danneggiato dalla prova di durezza Vickers.
Vale, ad esempio, la durezza Vickers della parola "45h" in
viti con
esagono o "14H" e "22H" in viti con intaglio e in
odontoiatria in
leghe dentali . Le classi di resistenza 14H, 22H, 33H e 45H si ottiene dividendo i valori di durezza di 10, che corrispondono quindi Durezza Vickers HV (min.) di 140, 220, 330 e 450
Leghe dentali [ Modifica ]
La durezza di Vickers dentale metalli per leghe di metallo prezioso con il carico di prova HV5 (5 kgf corrisponde 49,03 N) e
NEM misurata leghe con HV10.
Per leghe dentali tre valori di durezza si possono distinguere:
- s = morbido, durezza della lega come ricevuto e dopo ricottura
- una indurito =, durezza della lega ad un trattamento termico specifico = "ricompensa"
- g / b = remunerazione sé: durezza della lega, che può essere ottenuto mediante raffreddamento lento dopo fusione può
Durante l'esecuzione della prova è di assicurare che il tempo di permanenza del carico di prova è 10-15 s. Il campione deve essere saldamente fissata e l'area di prova di essere assolutamente perpendicolare alla direzione di prova. Dirt, ecc devono essere rimossi. Il test ha avuto successo, se i bordi dell'impronta e tutta la parte superiore della piramide vengono premuti nel centro. In pratica, si consiglia di eseguire le impressioni più, il massimo. e min. Valore di queste misurazioni essere ignorato e per determinare la media dei rimanenti.
Prova di durezza Knoop [ Modifica ]
Una variante del test di durezza Vickers, prova di durezza Knoop è (DIN EN ISO 4545-1 a -4: Materiali metallici - Prova di durezza Knoop), dal fisico americano e ingegnere
Frederick Knoop stato sviluppato 1939a
[6] La in Vickers Test punta di diamante in equilatero la prova Knoop una forma romboidale. Gli angoli di punta sono 172,5 ° e 130 ° per il tempo corto della pagina. Solo la diagonale lunga della rientranza viene misurata. Il test Knoop viene spesso utilizzato per materiali fragili come
la ceramica o
materiali sinterizzati , la misurazione della durezza dei sistemi di rivestimento, che rappresenta il metodo più accurato di misurazione

Shore Prova di durezza [ Modifica ]

Dispositivo portatile per la prova di durezza di elastomeri: Proprio sotto l'ago per la penetrazione

6 Piastra mm di gomma di spessore nella metro, circa l'ago che penetra il tester di durezza Shore
Per elastomeri [ Modifica ]
La durezza Shore sviluppato nel 1915 dalla American
Shore Albert [7] , è un parametro materiale per
elastomeri e materie plastiche, e si trova nelle norme DIN 53505 e DIN 7868 Il nucleo del durometro Shore costituito da un perno caricato a molla in acciaio temprato. La sua profondità di penetrazione nel materiale da testare è una misura della durezza Shore, su una scala da 0 Shore (2,5 penetrazione mm) a 100 Shore (0 mm di profondità) viene misurata. Un numero elevato indica una elevata durezza. Con un tester di durezza Shore di un dispositivo aggiuntivo può essere impiegata per il campione da misurare con una forza di 12,5
Newtons a Shore A 50 Shore D o presse di Newton sulla tavola di misura. Nel determinare la durezza Shore, temperatura svolge un ruolo più importante nella determinazione della durezza dei materiali metallici. Così qui, la temperatura obiettivo di 23 ° C è la temperatura intervallo di ± 2
K limitata. Lo spessore del materiale deve essere di almeno 6 mm. La durezza della gomma da rete (= gomma reticolata debolmente morbida, gomma altamente reticolato =) determinata. Ma il contenuto di riempitivo è cruciale per la durezza di un articolo di gomma.
- Shore A è indicato per elastomeri morbido, come misurato da un ago con una punta smussata. La faccia di estremità del tronco di cono ha un diametro di 0,79 millimetri, l'angolo di apertura è di 35 °. Peso della base: 1 kg, tempo di sosta: 15 palmari s di solito devono essere letti immediatamente quando viene premuto sul campione, il valore visualizzato diminuisce con più tempo di mantenimento.
- Shore D viene specificato quando i denti elastomeri come misurato con un ago, che si rastrema con un angolo di 30 ° ed ha una punta sferica con un raggio di 0,1 millimetri. Peso della base: 5 kg, tempo di sosta: 15 s
Le misure sono anche trovato a terra e B Shore C, anche se sono raramente usati. Questi test ogni combinare il tronco di cono del Shore dell'inchiesta A e Shore D con il carico di prova altro.
Un metodo simile è metrologico determinare la
IRHD = "International Rubber Hardness Degree", in tedesco anche
microdurezza chiamato.
Per i metalli [ Modifica ]
Questo metodo si basa sul principio che una pallina cade al pezzo (o un albero con una punta a sfera) rimbalza più o meno, a seconda della durezza del pezzo e l'altezza di caduta. È poco utilizzata, in quanto, anche se è un metodo molto semplice, la precisione sia la massa del pezzo (per piccoli pezzi può facilmente venire a scivolare) e dipende dall'asse verticale perfetta del caso. La misurazione della durezza è espressa in punti Shore ed è solo standardizzato per cilindro grande terreno.
Prova di durezza Barcol [ Modifica ]
Il Barcol è una scala di durezza di
materie plastiche rinforzate con fibra di vetro (FRP). Secondo DIN EN 59 è come una durezza Shore dell'aiuto di uno strumento portatile e un
tronco di cono con una cima piatta determinata.
Prova di durezza Buchholz [ Modifica ]
La durezza Buchholz è per
vernici utilizzate, e può essere liscia, almeno (10 + profondità di penetrazione micron) vengono usate spesse non elastiche rivestimenti. Per determinare la durezza Buchholz secondo DIN 53 153, ISO 2815, il tester Durezza Buchholz, che consiste in un tondo, ruota tagliente (= doppio tronco di cono) e un contrappeso, previsto per 30 secondi sulla superficie orizzontale, e quindi la lunghezza impressione 20 con una ingrandimento volte microscopio misurata. La durezza Buchholz viene quindi ottenuta utilizzando la seguente formula
[8] :

Per una migliore visibilità della lunghezza del corpo impressione è fornito con una lampada ad un angolo di 30 ° rispetto al piano perpendicolare al corpo illuminato impressione, per cui il sito impressione dal resto finitura molto brillante.
Leeb Prova di durezza [ Modifica ]
La prova di durezza Leeb è stato applicato nel 1978
[9] e misura l'energia applicata sul rimbalzo.
Durezza Mohs di prova [ Modifica ]
Il valore di durezza può essere determinata solo dal confronto diversi materiali o stati materiali.
Tessuti rigidi scratch morbido. Questa intuizione si basa sulla prova di durezza
Mohs Friedrich (1773-1839), utilizzati principalmente nel
mineralogia viene utilizzato. Mohs, un geologo graffiato, diversi minerali contro l'altro, così allineandoli secondo la loro durezza. Con l'assegnazione di valori numerici per esemplari minerali diffusi e quindi facilmente raggiungibili portato ad una
scala ordinale , la scala di Mohs, che si trova nella mineralogia e geologia fino ad oggi in un servizio ampio. Le differenze di durezza tra i minerali riferimento individuali sono non lineari. Informazioni sulla durezza dei minerali sempre riferimento alla scala Mohs, se non diversamente specificato. Nella lista per il confronto è anche chiamato assoluta durezza abrasiva durezza
Rosiwal che caratterizza il lavoro di macinazione della sostanza e dà una migliore impressione di durezza dei rapporti reali. Entrambe le scale di durezza sono senza unità. Inoltre, nella tabella, la durezza è indicato dal metodo Vickers. Essa riflette il meglio con prova di durezza standard di oggi.
Per quanto riguarda la disponibilità e l'assistenza a lungo termine di minerali come
gemme spesso una classificazione qualità più scadente è data. Minerali dom applicare la durezza Mohs 1 e 2 come morbido, da 3 a 5 medio-duro, e tutti i minerali sulla durezza Mohs 6 sono descritti come duro.
[10] [11]
Minerale | Durezza (Mohs) | durezza assoluta | Durezza Vickers HV in | Commento | Immagine |
Talco | 1 | 0,03 | 2,4 | con unghia schabbar |  |
Gesso o salgemma | 2 | 1,25 | 36 | graffiato con l'unghia |  |
Calcite (calcite) | 3 | 4,5 | 109 | graffiato con moneta di rame |  |
Fluorite (fluorite) | 4 | 5.0 | 189 | con coltello ben resistente ai graffi |  |
Apatite o manganese | 5 | 6,5 | 536 | con il coltello ancora resistente ai graffi, il più duro tessuto umano lo smalto dei denti ha questo grado di durezza [12] | 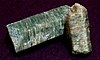 |
Ortoclasio (feldspato) | 6 | 37 | 795 | graffiato con file in acciaio | 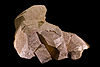 |
Quarzo | 7 | 120 | 1120 | graffi finestra di vetro |  |
Topazio | 8 | 175 | 1427 | |  |
Corindone | 9 | 1000 | 2060 | Una varietà di corindone è zaffiro . |  |
Diamante | 10 | 140000 | 10060 | più difficile in natura minerale, solo a se stessi e (in caso di riscaldamento) di nitruro di boro resistente ai graffi. Nel frattempo, pochi, prodotti artificialmente, materiali noti più duri, tra cui: ADNR . |  |
Prove di durezza più speciali [ Modifica ]
Inoltre, alcuni particolari metodi di prova di durezza sono comuni:
- La prova di durezza universale nel 2003 è stata ribattezzata la durezza Martens prova e nella norma DIN EN ISO 14577 (Materiali metallici - rientro di prova strumentato per la durezza dei materiali e dei parametri), istituito
- Quando la pressione di prova a sfera secondo EN ISO 2039-1 per le materie plastiche che lavorano con le palle di 5,0 mm di diametro, un carico iniziale di 9,8 N e carichi di prova di 49,0, 132, 358 o 961 N. La profondità di penetrazione deve essere compreso tra 0,15 mm e 0,35 mm. Ciò si traduce in un carico di prova ridotta e infine viene palla indentazione durezza HB lettura in N / mm ² o calcolata da una tabella.
- Carbone di Index Hardgrove .
- Nanoindentazione
La durezza Mohs e la durezza assoluta sono variabili adimensionali.
La disposizione corretta fisica dell'unità Vickers e prova di durezza Brinell sarebbe 1 N / m o 1 N / mm ². Ma si deve notare che questo metodo di prova all'inizio del 20 Secolo sono stati sviluppati e da allora sono stati standardizzati in norme più dettagliate e internazionalizzato. Che ha una notazione un po 'astratto per i fisici dei valori di durezza e il risultato unità. Come unità di durezza è l'abbreviazione del metodo di prova e la prova è data.
Alcuni esempi illustrano questo:
- Durezza Vickers di prova:
- 610 HV 10
- in cui:
- 610 = valore di durezza
- HV = processo
- 10 = Forza di prova in newton
- Prova di durezza Brinell:
- 345 HBW 10/3000
- in cui:
- 345 = valore di durezza
- HBW procedura = (informazioni come HB, HBS sono obsoleti.)
- 10 = sfera di diametro D in mm
- 3000 = Forza di prova in newton
- Con un carico che richiede più di 15 secondi, il tempo di caricamento può anche essere specificato. Esempio: 210 HBW 5/750/60
- 58 HRC
- in cui:
- 58 = valore di durezza
- HRC = metodi di prova
- In precedenza la forza è stata misurata in newton. Una forza chilogrammo corrispondeva al peso di un chilogrammo. La conversione dell'unità della forza da Pond sull'unità Newton aveva. Correzione delle formule utilizzate per calcolare il risultato durezza Questa correzione è già inclusa nell'articolo. Viene utilizzato per la determinazione del valore di durezza forza dell'unità Newton e il fattore di correzione, il risultato è lo stesso con l'uso del kilopond potenza. Questo ha il vantaggio che i vecchi, a "Kilopondzeiten" valori di durezza determinati restano valide.
- Quando si specifica la procedura per motivi pratici Kilopond ancora utilizzati perché anche i numeri possono essere utilizzati.
Tempra e la lavorazione [ Modifica ]
La durezza dell'acciaio può essere influenzato durante la produzione - si veda anche
disagio .
Sopra una durezza di circa 60 (durezza Rockwell HRC) di solito finiscono le possibilità di
taglio lavorazione con definiti taglienti delle superfici, vale a dire da tornitura, foratura o fresatura. Harder superfici devono tagliare o
erosa , stai parlando di lavorazione con taglio geometricamente definito.
Rivalutazione [ Modifica ]
Quando si tratta di diversi metodi di prova di durezza, è spesso necessario rivalutare il valore di durezza misurata di un metodo in un metodo diverso, o resistenza alla trazione. Per questo motivo, sulla base di una pluralità di confronti tra i valori empirici sono stati determinati Umwertungstabellen creati e standardizzato nella norma pertinente (EN ISO 18.265 (precedentemente DIN 50 150)).
Importante per diversi materiali e diverse fasi di trattamento termico sono tabelle diverse. I gradi sono compresi nella norma EN 18265 anche elencato.
Il seguente Umwertungstabellen può quindi essere considerato solo come guida. Una rivalutazione standardizzata corrispondente norma deve essere utilizzato. Se ci si sposta, ma nella progettazione di componenti, i limiti del possibile, delle dichiarazioni rese nei metodi di normalizzazione e di ipotesi spesso non sono sufficienti a garantire una corretta interpretazione e l'esame.
Rivalutazione | Fattore |
 |  |
 |  |
 |  |
 | (Nel campo di basso carico) |
 |
Acciaio (bcc - Fe matrice) | 3,5 |
Cu e lega di rame ricotto | 5,5 |
Cu e Lega di rame lavorato a freddo | 4.0 |
Al e Al-lega | 3,7 |
 | Tabella di conversione manca seguenti informazioni importanti: Non è specificato, (utilizzato) per cui l'acciaio (Es. S235JRG2?), i valori di resistenza. La dichiarazione sui "diversi tipi di metallo duro" è troppo vago. (Wahrsch e sbagliato.) Potete aiutare Wikipedia, permettendo loro recherchierst e incollarlo , ma per favore non copiare testi stranieri in questo articolo. |
Tabella di conversione [13] per la resistenza alla trazione, Brinell [14] -, Rockwell, durezza Vickers.
Resistenza alla trazione (per acciai al carbonio e basso legati.) | Brinell | Rockwell | Durezza Vickers |
MPa | HB | HRC | HRA | HRB | HV |
- | - | 68 | 86 | - | 940 |
- | - | 67 | 85 | - | 920 |
- | - | 66 | 85 | - | 880 |
- | - | 65 | 84 | - | 840 |
- | - | 64 | 83 | - | 800 |
- | - | 63 | 83 | - | 760 |
- | - | 62 | 83 | - | 740 |
- | - | 61 | 82 | - | 720 |
- | - | 60 | 81 | - | 690 |
- | - | 59 | 81 | - | 670 |
2180 | 618 | 58 | 80 | - | 650 |
2105 | 599 | 57 | 80 | - | 630 |
2030 | 580 | 56 | 79 | - | 610 |
1955 | 561 | 55 | 78 | - | 590 |
1880 | 542 | 54 | 78 | - | 570 |
1850 | 517 | 53 | 77 | - | 560 |
1810 | 523 | 52 | 77 | - | 550 |
1740 | 504 | 51 | 76 | - | 530 |
1665 | 485 | 50 | 76 | - | 510 |
1635 | 473 | 49 | 76 | - | 500 |
1595 | 466 | 48 | 75 | - | 490 |
1540 | 451 | 47 | 75 | - | 485 |
1485 | 437 | 46 | 74 | - | 460 |
1420 | 418 | 45 | 73 | - | 440 |
1350 | 399 | 43 | 72 | - | 420 |
1290 | 380 | 41 | 71 | - | 400 |
1250 | 370 | 40 | 71 | - | 390 |
1220 | 376 | 39 | 70 | - | 380 |
1155 | 342 | 37 | 69 | - | 360 |
1095 | 323 | 34 | 68 | - | 340 |
1030 | 304 | 32 | 66 | - | 320 |
965 | 276 | 30 | 65 | - | 300 |
930 | 276 | 29 | 65 | 105 | 290 |
900 | 266 | 27 | 64 | 104 | 280 |
865 | 257 | 26 | 63 | 102 | 270 |
835 | 247 | 24 | 62 | 101 | 260 |
800 | 238 | 22 | 62 | 100 | 250 |
770 | 228 | 20 | 61 | 98 | 240 |
740 | 219 | - | - | 97 | 230 |
705 | 209 | - | - | 95 | 220 |
675 | 199 | - | - | 94 | 210 |
640 | 190 | - | - | 92 | 200 |
610 | 181 | - | - | 90 | 190 |
575 | 171 | - | - | 87 | 180 |
545 | 162 | - | - | 85 | 170 |
510 | 152 | - | - | 82 | 160 |
480 | 143 | - | - | 79 | 150 |
450 | 133 | - | - | 75 | 140 |
415 | 124 | - | - | 71 | 130 |
385 | 114 | - | - | 67 | 120 |
350 | 105 | - | - | 62 | 110 |
320 | 95 | - | - | 56 | 100 |
285 | 86 | - | - | 48 | 90 |
255 | 76 | - | - | - | 80 |